Influencing factors of steam consumption in oil press factory
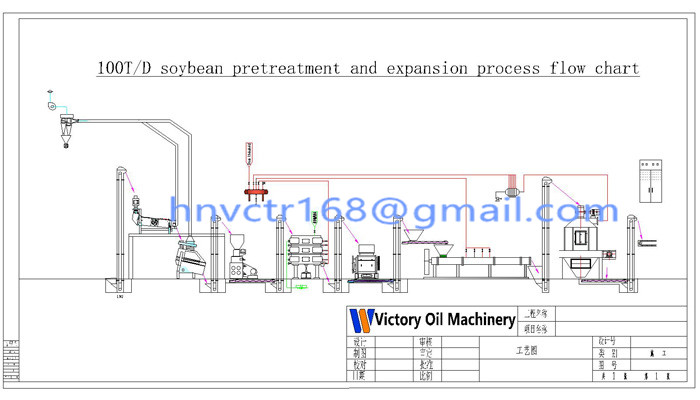
The cost of a single ton of steam consumption in a soybean crushing plant accounts for about 40% of the cost of soybean processing. Steam consumption is one of the important indicators to measure the level of production process equipment and management level of the plant. In the past two years, energy prices have risen, and competition among oil plants has been fierce. Reducing steam consumption has become the focus of improving quality and efficiency, as well as energy saving and consumption reduction. For the soybean crushing industry, in the past few years, external peers and internal groups have compared the production indicators over and under, and various consumption levels are different. The low steam consumption factories are close to 200kg/T of material, and the high is 265kg/T. The difference is 30%. The level of steam consumption is closely related to product yield, product quality, and other electricity and solvent consumption. Why is there such a big difference in steam consumption between factories? Does the very low consumption mean that the production process equipment level and management level are relatively high?
1. The influence of process equipment on steam consumption
1) Process and equipment selection affect the consumption index of production. For the same processing volume, the more equipment is used, the more heat equipment and pipes are used, and the more steam is used for transportation equipment. For example, a 3,000-ton processing plant will use two A quenching and tempering tower consumes more steam than a quenching and tempering tower. DT and DC are separated, which consumes more steam than a single DTDC.
2) During the equipment installation process, most of the heating equipment and pipelines are insulated, but some factories of the extractor, cold drying box, hot bean, and hot embryo conveyor are insulated, and some are not insulated, which also affects energy consumption .
3) Some factories have crude oil degumming and phospholipid drying equipment in the Solvent extraction workshop, while others do not. The steam statistics are different, which also caused some differences.
4) Some factories use steam power for the vacuum and stripping vacuum of the mixed oil evaporation and condensation system in the Solvent extraction workshop, and some factories use mechanical vacuum pumps. Different processes cause differences in steam consumption.
2. On-site management and maintenance
1) Poor site management, such as steam or water running and dripping, will inevitably affect steam consumption.
2) Whether the safety valves, pressure regulating valves, and pressure relief valves working in the workshop are working properly, the relevant instruments need to be adjusted regularly.
3) The heat exchange surface of the heat exchanger needs to be inspected and cleaned regularly. If there is fouling, it will affect the heat exchange effect.
4) The steam trap is checked regularly to see if there is internal leakage and is it working properly?
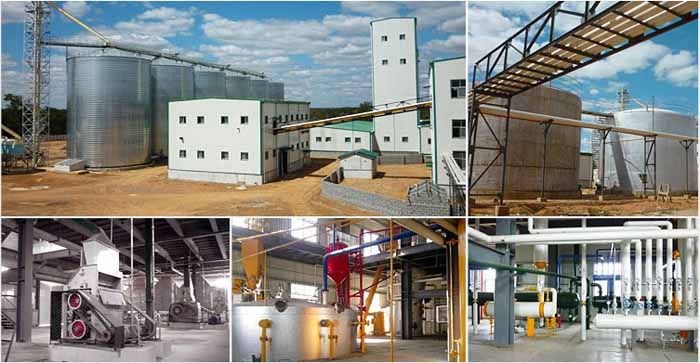
3. Waste heat utilization
1) The hot oil, condensed water, waste water, waste gas, etc. leaving the workshop entrain heat. Most of the factories' degummed oil or stripped crude oil, and the waste water discharged from the cooking tank have undergone heat recovery. Recently, many factories have recovered the heat energy of the hot air discharged from the DC and the hot air discharged from the expanded cold-dry box, reducing steam consumption.
2) Some factories use the flash steam of the steam condensate tank, and some use the waste heat of the condensate. At present, the use of steam condensate to heat the air heater and the preheating of the upper beans of the tempering tower has become a hot topic. Grease engineers Zhijia believes that it is not necessary to use the waste heat of the condensed water of the factory with its own boiler. For its own boilers, more attention should be paid to the quality of the condensed water. The condensed water is fully returned to the boiler room for recycling. It seems that the steam consumption in the oil press workshop is low, but when returning to the boiler room, it has to be reheated. The coal consumption has not changed, but the electricity consumption has increased.
4: Summary
The level of steam consumption in the soybean crushing plant is not a matter of the production workshop alone, but a reflection of the level of operation and management of the entire plant. Maintaining continuous production and high operating rates are important factors for the level of steam consumption. According to the law of conservation of energy, the energy required by the workshop depends on the heat taken away by the finished product, the heat discharged from the waste gas, and the waste water. The less the heat, the less the steam consumption of the workshop. As long as the above three aspects are well controlled, The steam consumption can be controlled within a reasonable range.
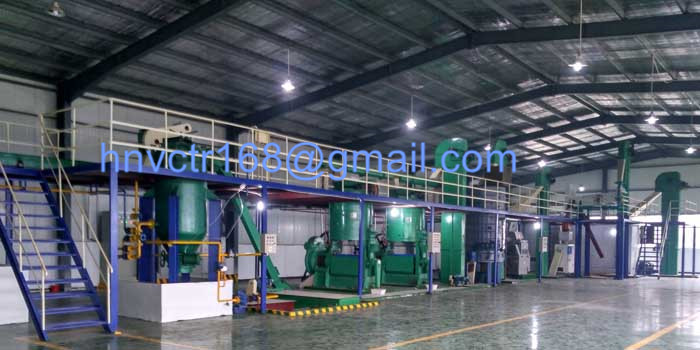
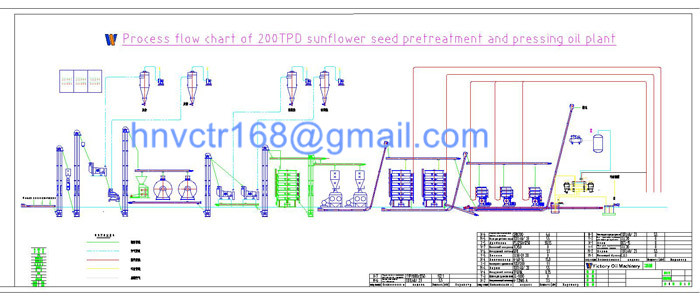